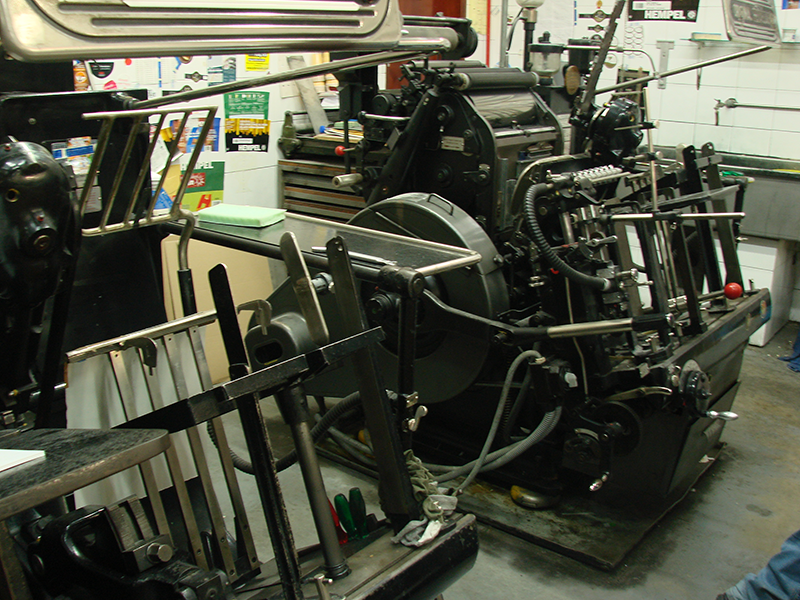
These old Heidelberg lead or letterpress printers are pure industrial archaeology, but they print die cuts and and hot gold.
The art of printing has two contradictory characteristics: it is one of the sectors most revolutionized by technology, in successive waves, in recent years; but it is also heir to a proud professional mastery of tradition and knowledge transmitted from successive generations of masters to apprentices.
Until almost the end of the twentieth century, a graphic ars professional would begin the career as an apprentice, often a child, and go up the qualifying steps to get to first officer, but each promotion was marked by a very difficult practical test organized by the union, under the responsibility of the older masters.
Thus, the graphics professionals maintained a place of great prestige among all professional classes, due to the careful training of their peers and a great professional pride that grew with these practices.
Several innovations (first offset printing, then the computerization of text composition operations, later digital printing, desktop publishing and the Internet) have changed the sector so much that an old graphic professional would hardly recognize it – except for the fact that paper is still printed. But certain traditional processes remain, stubbornly refusing to be dethroned (for now) by future technologies.
Hot gold and relief
For example, in some luxury work, hot gold printing is used, be it logos, coats of arms or headings. Neither offset nor digital printing can solve this problem. In offset printing there are special inks we call cold gold and cold silver, which come close, but they lack the true glitter of gold or silver.
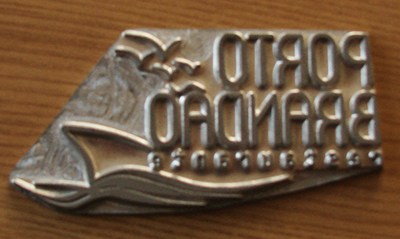
Zincography used to print hot gold. For those not accustomed to reading mirrored prints, what is written is "PORTO BRANDÃO - RESTAURANTE". The picture has to be mirrored so that the printed result shows "right".
Authentic print with gold uses a zincography (zinc engraving) heated with an electrical resistance that presses a gold film against the paper. As it is hot, the engraving leaves on the paper its image in molten gold. To deal with these prints, an old flatbed printer like the Heidelberg at the top picture is necessary, not to print with lead types, but to use the print board to support the heated engraving.
Another application of the old machines is relief printing. This is obtained by pressing the paper against a zincography, so that the raised engraving is marked on the paper. Among other applications, this is the process used to create white seals.
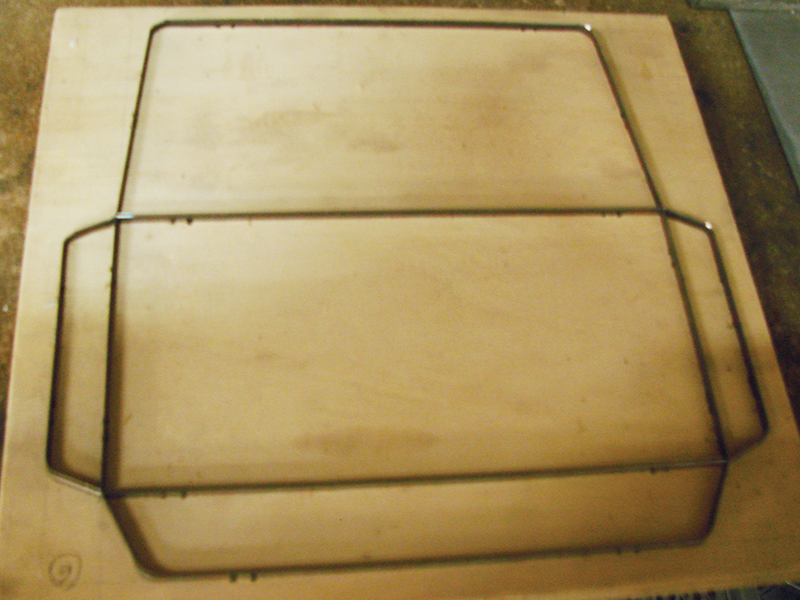
Steel-rule die for a large envelope (paper bag). The steel blades are mounted on a wooden base. The outside ones are taller and sharper, to cut; the inner ones are shorter and blunt, to just crease the paper.
Cutting & creasing
But the great utility of these old and extremely robust machines is in what we in the art call cutting & creasing. We use to think of printing as producing pieces of rectangular or square paper, but it is often necessary to cut the final product in more creative ways: for example, round cornered cards, circular glass bases, Christmas cards in the trim of Christmas trees, folders for documents with their flaps, packages delivered flattened to be easily assembled in the factories to pack products.
So we use these machines to compress a blade mounted on a wooden board (we call it a steel-rule die) against the sheet of paper, making the necessary cut. The die includes, on its wood base, taller sharper blades to make cuts, but also shorter and blunter blades that only make creases, to facilitate the accurate folding of the piece.
Here we see a steel-rule die mounted in the board of the cylindrical Heidelberg, where the lead types original should have been. Here we have a document folder previously printed in offset.
The brute force required for cutting and creasing would destroy a modern offset machine, especially since these works are often printed on thicker cardstock. Good thing there are these machines from another era to use in this work!
UV varnish and lamination
Another common way to finish printed works is the matte or glossy UV varnish, or lamination (a thin plastic layer) also matte or glossy. When the UV varnish is localized, meaning printed on certain locations of the paper and not on others, it can show spectacular effects. These processes use offset, though we have now a concurrent digital process for a kind of localized varnish.
But despite the passion we have for the old printing methods, we are not stuck on the past. From the trade shows that we visit we bring innovative processes of digital printing that, once again, promise new feats and will turn upside down our business.
Nothing new... Because, in the end, it is necessary to innovate to bring